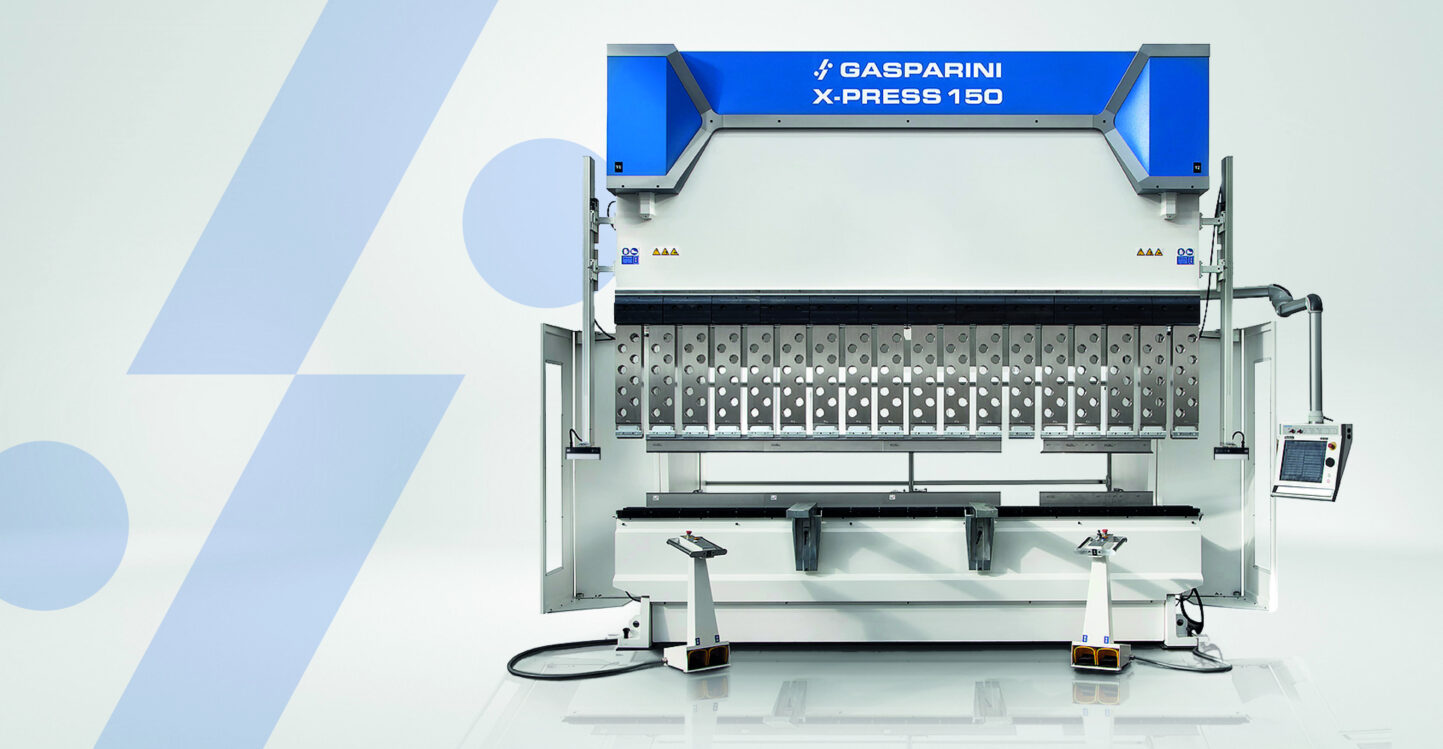
“We don’t offer plain machines. We study solutions to provide the best answer to everyone”. With these words, the CEO Andrea Guderzo reveals the Company focus.
For nearly 50 years Gasparini represents the Italian excellence in bending and shearing, with more than 8.000 press brakes and shears installed worldwide, and about 10.000 m2 production site.
Tailor made approach for your best solution
"Our work starts from the analysis of the customer's needs to identify the perfect solution for his needs." Andrea Guderzo explains.
Each project benefits from Gasparini's know-how for solutions that are always different and original. Attention to performance, quality and service are the pillars on which the company bases its strategy. Gasparini's approach, starting from this assumption, has always been oriented to propose perfectly integrated and highly efficient solutions for each reality.
Its first and foremost Research Lab are its customer’s production workshops, design offices and meeting rooms. That’s why its products are always born in response to specific and real problems, be it technical or organizational in nature. It’s no accident that they invest 10% of their turnover in innovation: “That’s the only way we can help companies to become more competitive”.
Gasparini in recent years has changed and embarked on a path of very profound change, focused mainly on the production of high value-added machines that require novelty and strong product customization. It has decided to take care of these customers because it believes that the market is looking for new ways to work. It has chosen to listen to all those customers having clear ideas on their growing opportunity, so as to support them in reaching their targets.
Basically, it has changed its point of view: “listen and not force”.
The importance of ecology, the power of research
"For us, custom means finding the ideal solution to make bending and cutting sheet metal a quick, precise and reliable process, reducing consumption and costs.” the CEO continues. In this way Gasparini aims to design what the customer really needs, ensuring durability over time and contributing to the eco-sustainability of its products. Today, in fact, all this is a must for an attentive and responsible society: Gasparini has always respected ecological principles and was among the first to employ special water-based paints and steam washing machines for cleaning and degreasing instead of common chemical products. It has always been complying with the laws for environment protection, developing a production system with respect for ecology.
Thanks to its constant engineering research, Gasparini is qualified as a Research Laboratory by the MIUR that offer state-of-the-art in shearing and bending. It is precisely because of these studies that it has detected the trend of shrinking lot sizes: from a few large orders, there has been a shift to a large number of small orders, often very different from each other, down to the so-called "lot 1". Even those with their own products are not sheltered from this trend, given the increasing demand for customization. To maintain sufficient margins in these working conditions, it is essential to minimize waste and inefficiencies in terms of both material and time.
Artisans of quality
The quality of the Company is granted by the permanent research and development activity for product’s innovation and operator’s safety. Skilled operators and employees allow for maximum customization and an efficient assistance. It takes its team’s cultural assets very seriously. Most of its staff has a technical education and experience, at all company levels. It invests a significant amount of time and resources to bring to market more efficient and precise metalforming technologies, to offer its customers the best solutions available.
Gasparini goes further by always experimenting with new solutions. A case in point is its latest patents: Gasparini real-time adaptive crowning, GPS4 spring-back correction and angle measurement system, Gasparini pneumatic clamping and AirSlide tool adapters for quick setup, and Reflex digital frame deformation compensation system.
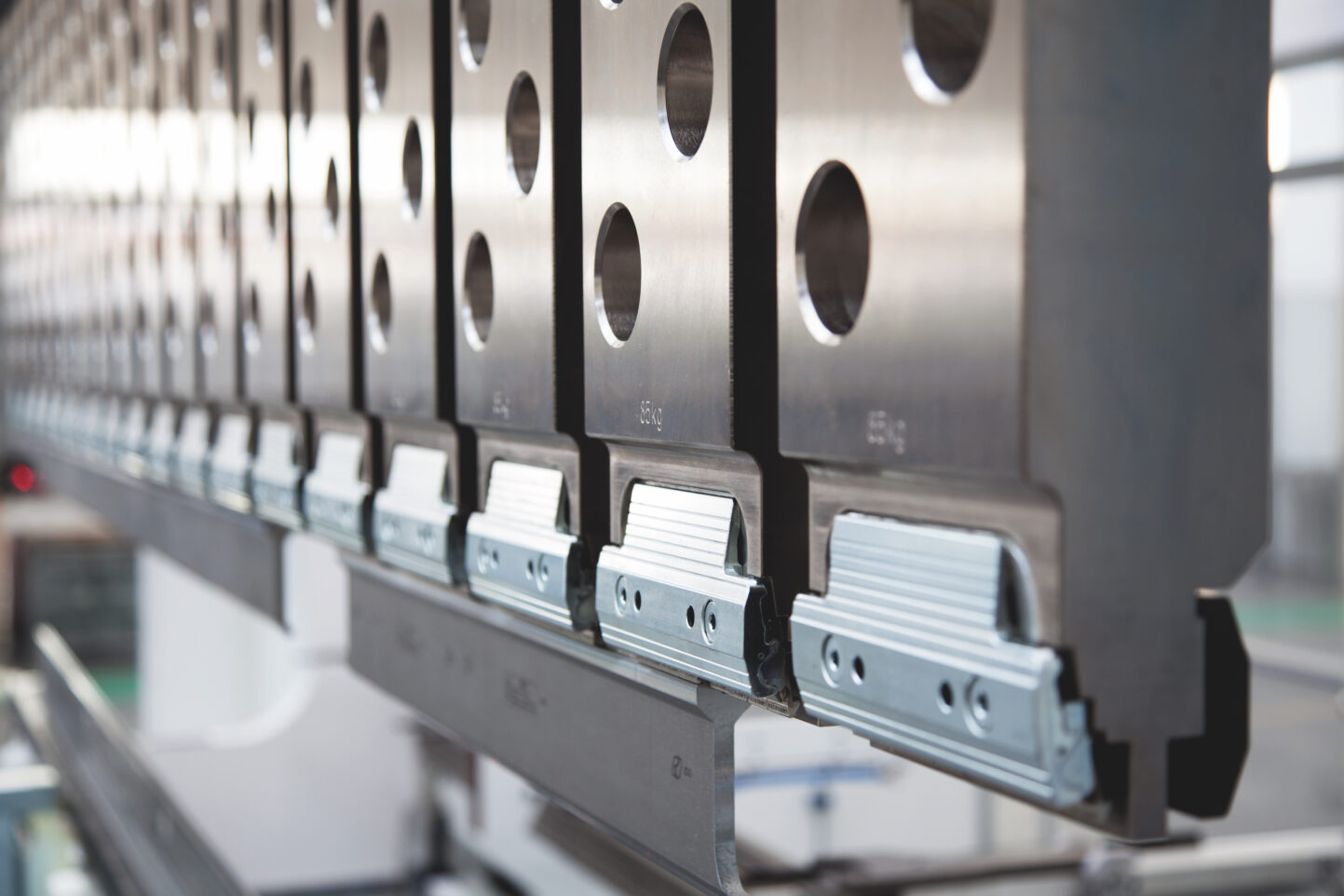
Big dreams become big goals
“We want to be regarded as the most authoritative actor in the sheet metal working sector. We aim to become more and more the point of reference on theory and practice of bending and cutting.”, says Andrea Guderzo.
That’s why its mission and vision are the quintessence of what it is, of something unique and unimitable.
All of them at Gasparini are devoted to the satisfaction of its customer, and always take its partners’ and its end user’s advice to heart. The Company has the experience but it also has the dinamicity of a startup business, because its main goal is to improve performances and exceed expectations.
The road to the Digital Factory
In addition, Gasparini's press brakes have been certified by the Pordenone Technology Pole as complying with Industry 4.0 recommendations. There are several key principles that guide the Company in this regard. The first is interconnection; in fact, open and robust communication standards allow Gasparini's press brakes and guillotine shears to connect to other machines and information systems. Then there is remote control, whereby CNCs can be interfaced with ERPs and databases, as well as perform advanced functions through a simple and intuitive user interface. TeleLink enables remote control of press brake operations and remote maintenance. In addition, everything is always under control thanks to a series of sensors to measure material characteristics and working parameters, which will be made available to data collection and reporting tools.
All information and data is then collected in dedicated software that allows it to be translated into useful information such as quality control, predictive analysis, and cycle times.
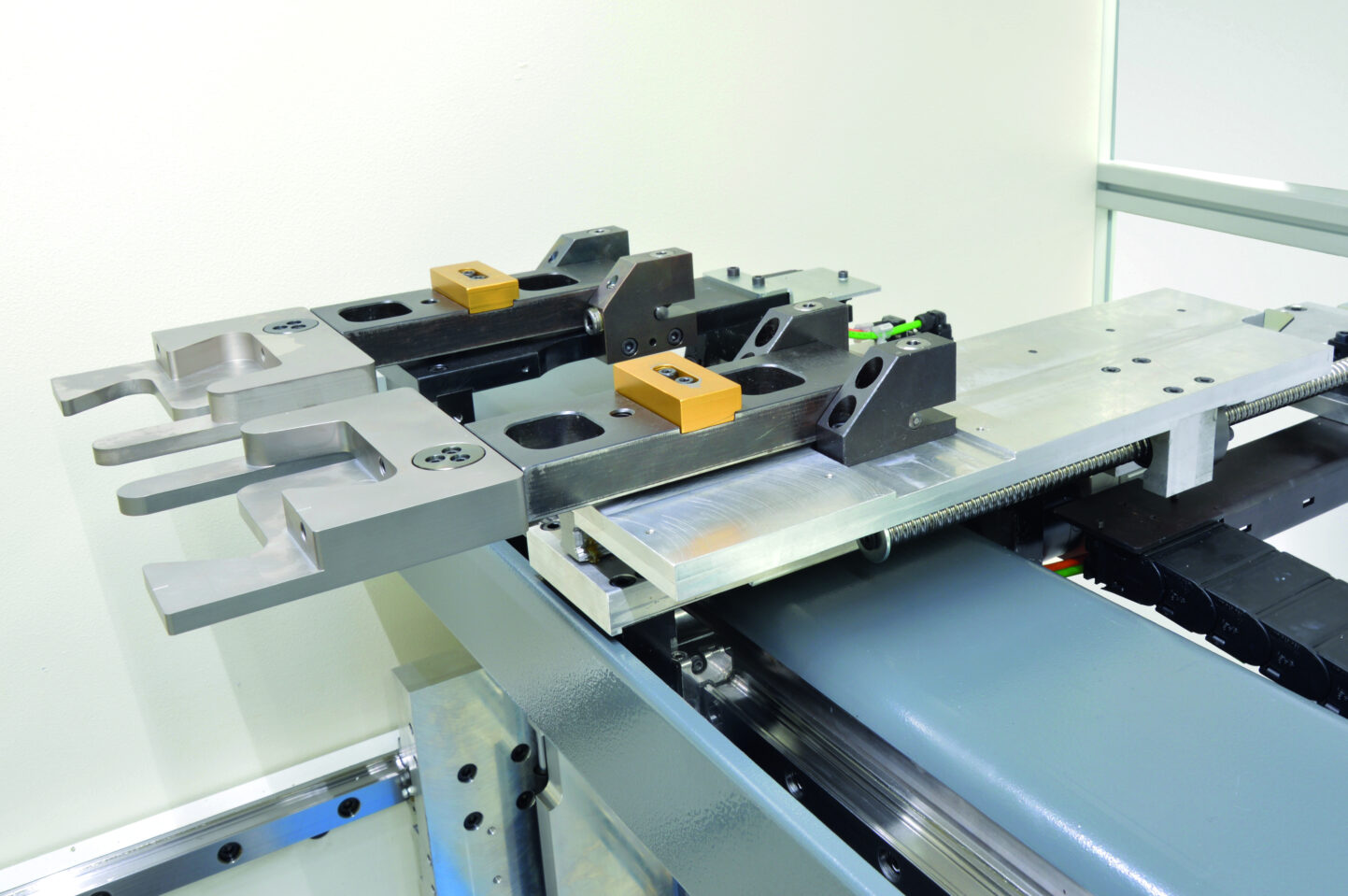
Much more than a product
Gasparini offers three main product platforms: press brakes, guillotine shears, and automated lines. All products are positioned at the high end of their specific market, providing a significant technological content, a robust design, together with an user-friendly configuration and a wide range of options and accessories, to customize the machine according to your needs.
With this purpose, it has introduced in its organization the “Tech Center Division”, formed by a team of specialists, fully dedicated to analyzing the specific customer needs and to providing the best solution.
One of the products that symbolizes the tailored approach is the SuperCustom set-up, a press brake with light and stroke customized to the extreme, specifically for customers who make deep boxwork such as tanks and casings. Another example is a shear made for a large global steel mill: to meet restrictions on occupied space, the electrical panel was moved from the side to the area under the bench. Also for another customer, a shear was made with a wealth of accessories such as side discharge of cut pieces. But the most significant example remains the automated bending lines, such as the one for making radiant panels.
Returning to the X-Press SuperCustom press brake, it is a product that is the result of listening to and working with companies. "We wanted to create a tool that could make deep profile bending an easier, more precise and faster process" Andrea Guderzo continues.
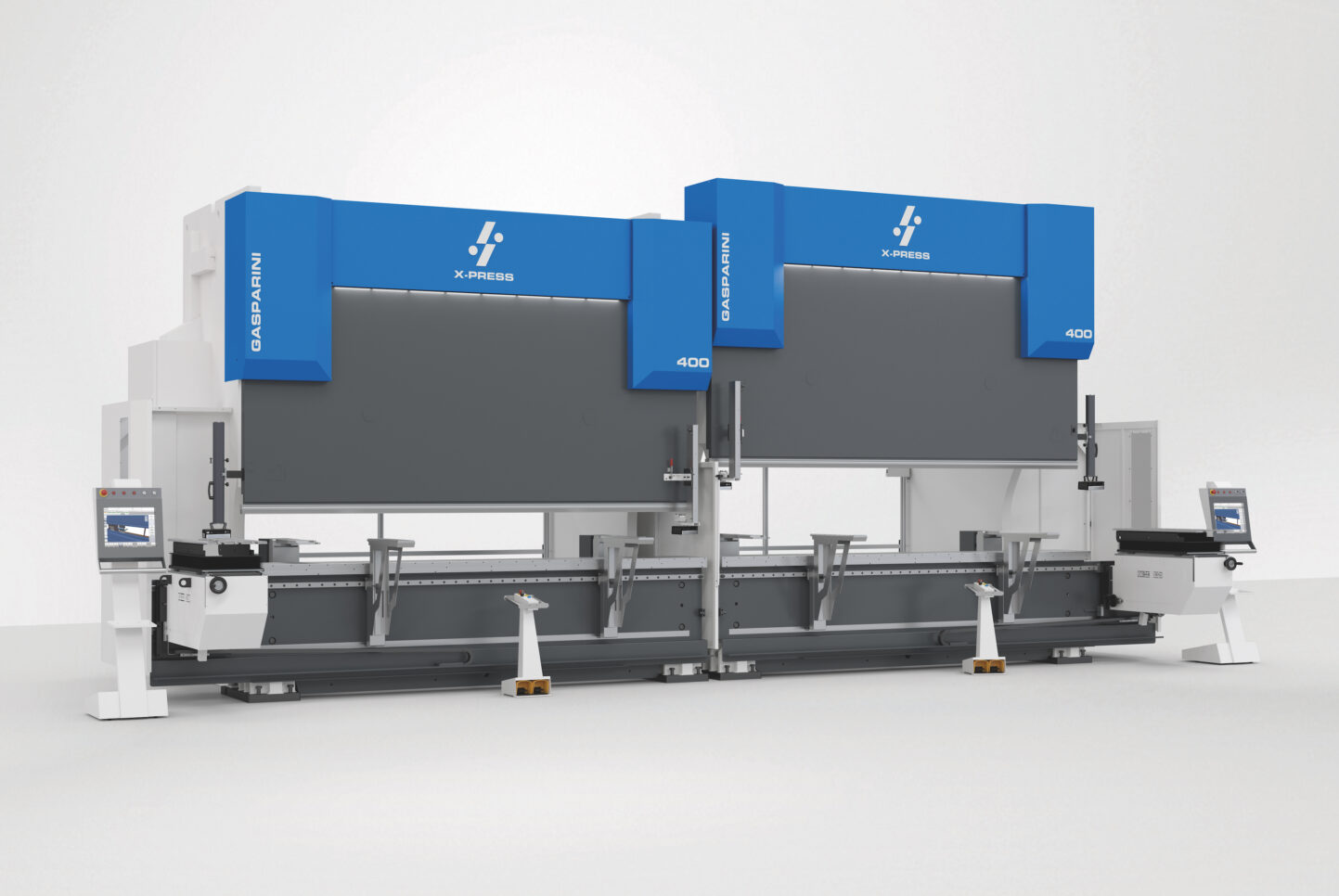
With its offerings, expertise and experience, Gasparini is the ideal partner for your projects.
When you choose Gasparini, you choose to shape your ideas.