As the sheet metal industry transitions to industry 4.0, the demand for greater, and more sophisticated levels of machine and process automation continues to grow. Press brake guarding technology has seen significant advancements in safety and functionality in recent years, and as systems and machines become increasingly complex, the need for automated guarding is now more important than ever.
Imagine a press brake with a fully autonomous guarding solution where there is absolutely no interaction required by the operator to adjust, setup or configure anything. In addition, what if the guarding functions could be automatically optimised according to the profile of the part to be formed, so that bends could be made with maximum efficiency. This level of automation is soon to be realised as press brake manufacturers adopt the next generation of advanced safety and guarding technologies.
When you think of press brake guarding and safety, there has been a general assumption that to achieve a high-level of operator safety, there is a trade-off between safety and productivity where compromises must be made in terms of machine performance and production output.
Guarding systems generally require adjustment, setup and checking prior to operating the machine, plus to some extent, there will be a level of interference between the machine operator, the work piece, and the guarding device. This creates situations where the protective area becomes obstructed which results in interrupted cycles, additional foot pedal presses and excessive slow speed operation. All these factors combined, increase the time to setup the machine for production and the time to manufacture each part.
Although, in the past, this sacrifice of productivity in the name of safety was often the case, advancements have been made in machine safety and guarding technologies, especially over the past decade. These newer and more advanced technologies have narrowed the gap between safety and productivity, leading to significant improvements not only in production speed and efficiency, but also in the way that machine operators interact with the press brake and its associated guarding and safety systems.
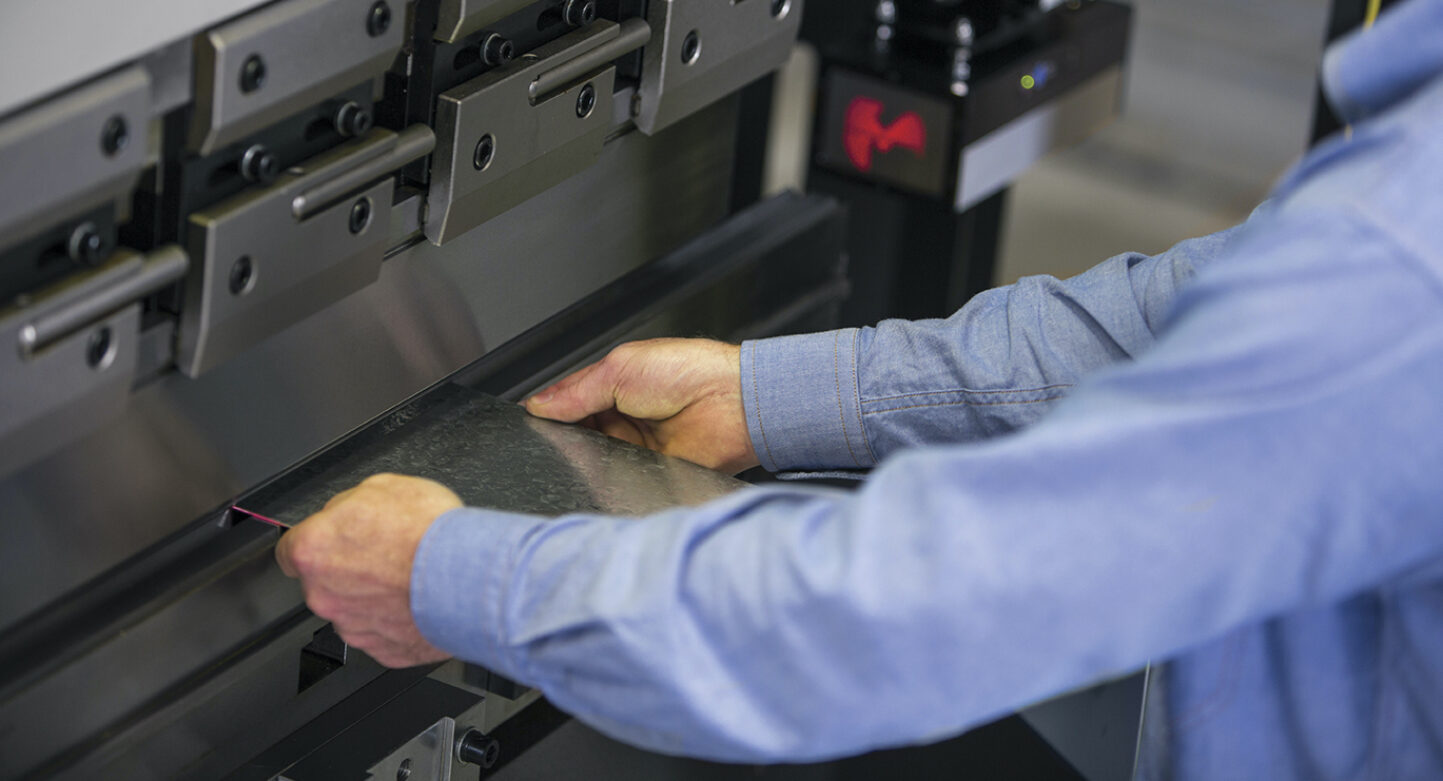
Even with today’s state of the art safety and guarding systems, press brakes remain hazardous machines, and the risk of an accident leading to operator injury, while drastically reduced, can still occur. There is a reliance on qualified press brake operators being trained in all general aspects of machine safety as well as being trained in the safety and guarding systems. This includes manual adjustment, setup and checks that need to be performed before the machine is operated. Even with many of the newer guarding technologies that feature a level of motorised adjustment, some level of setup or checking needs to be performed, and this responsibility lies with the machine operator.
With any manual adjustments to the optical guarding, the operator is required to reset the position of the device relative to the newly installed tooling. The process is usually performed by using some form of alignment tool or fixing a magnetic card or template to the punch. This acts as a guide for the operator to manually adjust and align the optical system with the installed tooling. Since this is a manual process, the responsibility is on the operator to make the correct adjustment, or if the adjustment is made incorrectly, there needs to be some additional checks or tests in place to identify it is incorrect. Failure to correctly adjust or identify an incorrect setup, could expose the operator to additional risk of injury.
Aside from the setup of the optical system, potential safety issues can arise if the tooling or material parameters configured in the CNC bend program do not match the physical setup. If left unchecked, this could lead to a high-speed tool collision, or high-speed tool contact with the material, both of which expose the machine operator to possible danger and significant risk of injury, not to mention the potential for costly damage to the machine and tooling.
An automated solution would eliminate the need for any manual adjustments performed by the operator by automatically moving the mechanical and optical components into the correct position, then automatically making any necessary adjustments based on the tooling that had been installed. In addition, secondary processes would automatically check and confirm the positioning and setup, thereby ensuring that the machine is safe to operate.
So, what is autonomous guarding?
The ideal solution is where the operator turns on the machine, installs the tooling and starts bending parts – all without have to setup, adjust, or check any of the safety and guarding systems, and with very little or no interference when forming parts. It would be as if the safety and guarding is not even there, and the machine operator can get on with the job without any disruptions.
Modern laser-based guarding technology has evolved over the past two decades to address these issues, with advanced functionality that is designed to minimise or eliminate interference without reducing the level of safety and protection for the operator. While these advancements have seen significant improvements in efficiency and productivity, there is still a reliance on the machine operator having detailed understanding of the guarding technology, plus the knowledge and experience to manually configure the guarding system setup, operating modes, and functions to suit the part profile and bending sequence.
Streamlined configuration in the bend program can eliminate or drastically minimise interference with the sensing zone, which results in fewer pedal presses, no unnecessary stops in the bend cycle and significantly more time in high-speed, resulting in faster and more efficient manufacturing.
To achieve this requires a combination of high-level guarding technology coupled with optimal setup of the optical system, plus configuration of guarding modes and parameters in the CNC bend program. Without these actions, many of the benefits offered through the technology are not utilised, and therefore the potential productivity advantages are not fully realised. Unfortunately, most press brake operators never receive the level of training and knowledge required to optimise guarding to achieve optimal productivity. This is where a fully automated solution provides a significant benefit.
Embedded, automated solutions versus integrated systems
When purchasing a new press brake, consideration should be given not only to the safety and guarding systems on offer, but how, and to what level these systems are integrated by the manufacturer. Safety and guarding integrated at the factory are generally considered a better option compared to a retrofitted system after taking delivery of the machine. However, there is a distinct difference between a custom embedded solution versus an integrated system and how this plays a part in the automated functions.
An integrated system is where the press brake manufacturer sources several third-party components, often from different manufacturers or suppliers, and integrates them to work together to provide the necessary safety and guarding functions that satisfy the applicable safety standards and notifying body for the market in which the machine is sold. There is absolutely nothing wrong with this approach, however, it does present limitations that restrict the flexibility and customisation required for the manufacturer to achieve full automation.
On the other hand, an embedded solution is very different in that the safety and guarding elements in both hardware and software are customised as part of the inherent design of the machine. This approach allows significantly greater flexibility, especially when the machine manufacturer is using a proprietary CNC platform.
Press brakes designed with SmartLink, Autosense and BendShield technologies already offer a high-level of automation in the guarding processes that include automatic monitoring of machine performance, automatic mechanical and optical adjustment based on the tooling installed in the machine and defined in the bend program, the automatic setting and management of the muting process with respect to the programmed tooling and material, and finally, the ability to dynamically adjust the guarding configuration in the bend program.
The final step to full automation is optimisation of the guarding configuration in the bend program, and this is achieved in one of two ways. The first method is an automated learning process between the optical system and the CNC software, where the optical system detects the part profile during each bending cycle of the first part. Information is passed to the CNC, where the modes and parameters are automatically configured and saved. This results in the guarding configuration being automatically optimised, as opposed to the machine operator or programmer having to determine the most efficient setup and manually perform the process.
The second method of automation is where the CNC 3D programming software automatically processes the bending sequence of the part with reference to the protective zones to determine points of interference with the machine or workpiece (e.g., side flanges, back-gauge fingers, etc.), then automatically defines the guarding parameters and operating modes in the bend program.
Each method results in a fully automated solution that further assists the press brake operator by automatically streamlining the guarding configuration in the bend program to achieve maximum productivity and efficiency outcomes.
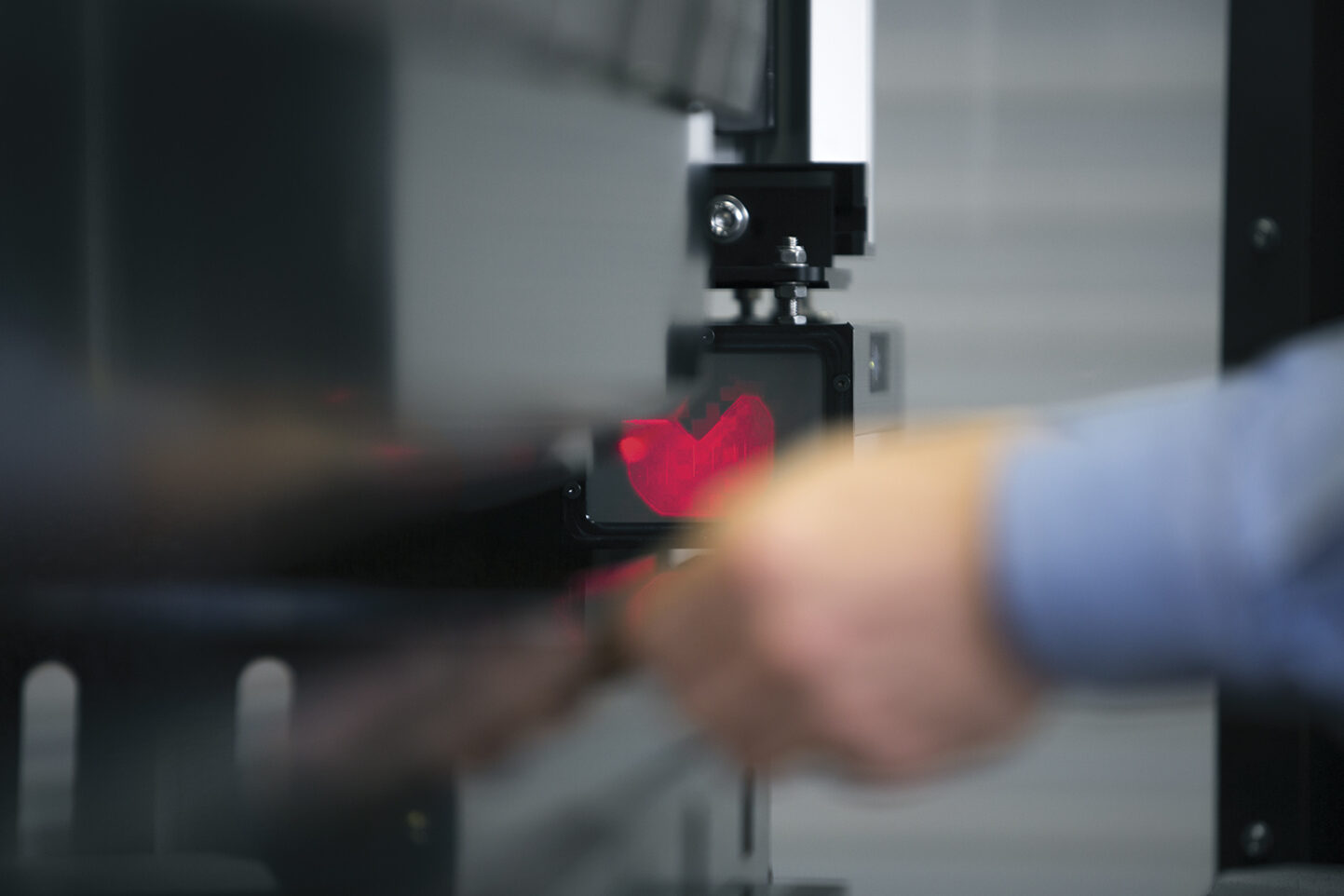
Additional benefits
In addition to the significant performance and productivity advantages, automated guarding provides some additional benefits. Depending on the type of safety and guarding system and the operator’s knowledge and experience, it could take anywhere from one minute to several minutes to adjust and setup the device, then test and check that the device and machine are safe to operate before production can commence. If the operator encounters an issue because of a setup or configuration error, then more time is wasted trying to resolve the issue. Automation eliminates these manual steps, saving valuable time and avoids the possibility of additional time lost due to incorrect setup.
When it comes to machine safety, the training of operators and supervisors is of upmost importance. Periodic retraining of existing staff and training of new staff requires an investment in time and resources, especially in workplaces with high staff turnover rates. Safety training covers many aspects of machine operation, including the basics of machine operation, hazards associated with various moving parts, proper tool installation, handling and setup, correct material handling, and an understanding of the safety and guarding system, setup, checking, and operation.
While automation is not intended to eliminate the need for operators to be trained, it does ensure that the press brake is always safe to operate, even if the operator is unfamiliar with the machine, and thereby takes much of the responsibility away from the operator. Manual processes are eliminated, so the machine is always safe to operate.
The technology to achieve full automation has now been developed and press brakes designed with fully autonomous guarding will soon be widely available.