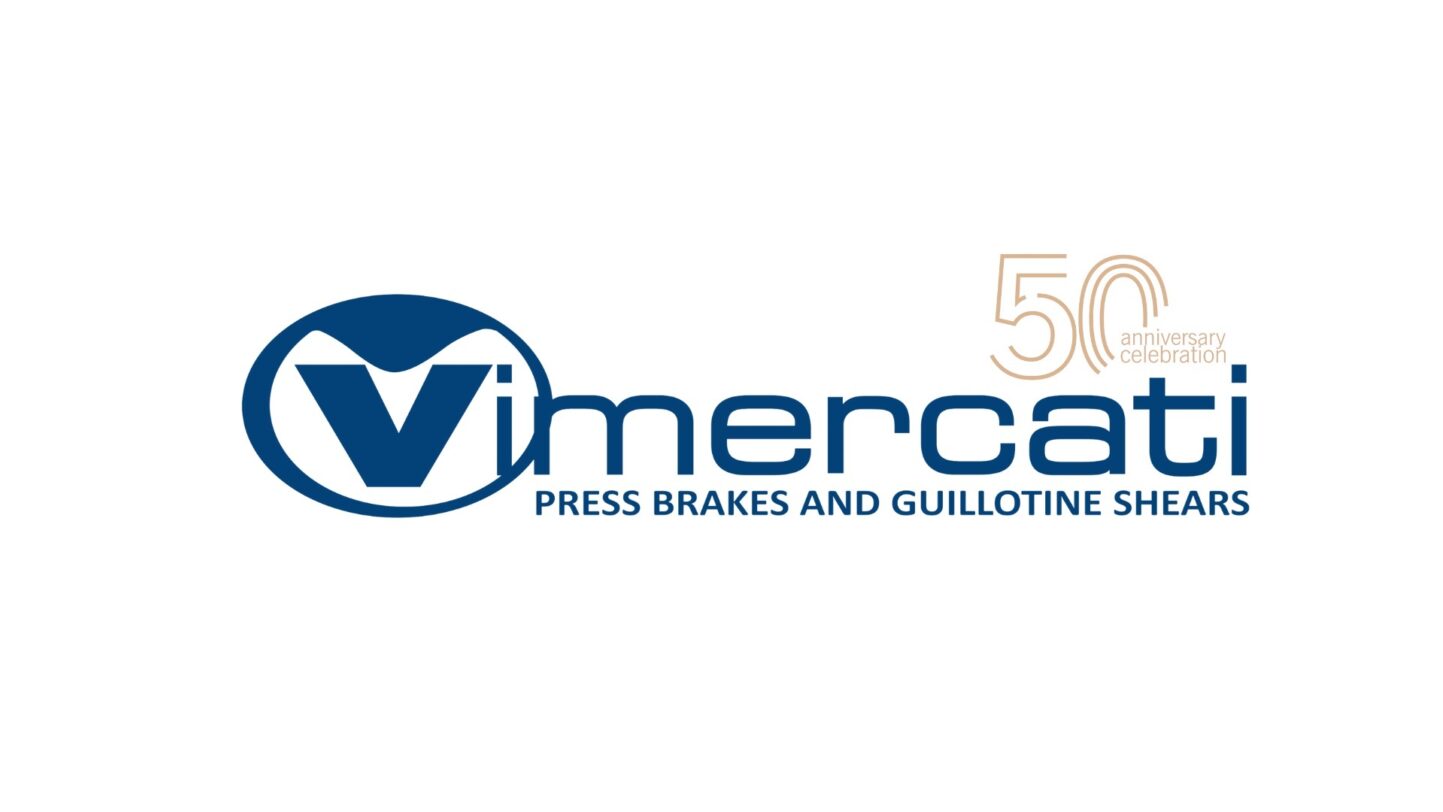
Vimercati was established in 1973: ever since it has been guaranteeing ongoing and prompt supply of machinery and technical assistance to its customers. Specialized in the production of press brakes, guillotine shears and sheet metal processing systems. With its decade-long experience on Italian and international markets, Vimercati offers reliable and top-quality products entirely made in its plants.
Its highly specialized staff takes care of the whole production process, from the purchase of raw materials to all the manufacturing phases combining the new opportunities offered by modern electronics and computing to create strong, high-tech, reliable, accurate and extremely flexible machines.
Vimercati offers a wide range of hydraulic and hybrid press brakes, starting from the smallest 30 tonnes x 1250 mm up to the 600 tonnes x 8050 mm, without stroke and opening limits along with a varied series of optional accessories. Tandem press brakes with various setups: with two or more press brakes with the same length and the same nominal bending forces; with two or more press brakes with different lengths and different bending forces. Along with the vast offer already available, we can design customized and specific solutions based on the production needs of individual customers.
Press brakes are equipped with: ACTIVE - HCL crowning system. One or more sensors, detects in real time the flexion, and instantaneously adjusts the deformations of the bench, allowing a perfect bending linearity. The cylinders of this crowning system are located in spherical housings that grant an excellent grip of the mechanical parts, avoiding at the same time any kind of wear and jamming during the working phase. Special mechanical solutions isolate the supports of the optical lines to check the linearity of the table and allow for perfect functionality of the Active HCL crowning system. The whole system is fully automatic and controlled from the CNC through dedicated software.
LAZER SAFE IRIS safety devices that manage, through a dedicated PLC and under top safe conditions, the speed change (fast approach – bending speed) at contact with the sheet metal. The LAZER SAFE safety devices are also available in a motorized version with automatic positioning managed by CNC control. LAZER SAFE IRIS PLUS devices can be installed on press brakes up to maximum two metres in length. In addition to the above features, they can measure, check, and correct the bending angle to obtain, right from the first piece, minimum precision tolerances regardless of any changes in thickness, strength and rolling direction. The system can be used in real-time mode with elastic return measurement for each single bend or in database mode, with elastic return value detected and saved in a customizable database.
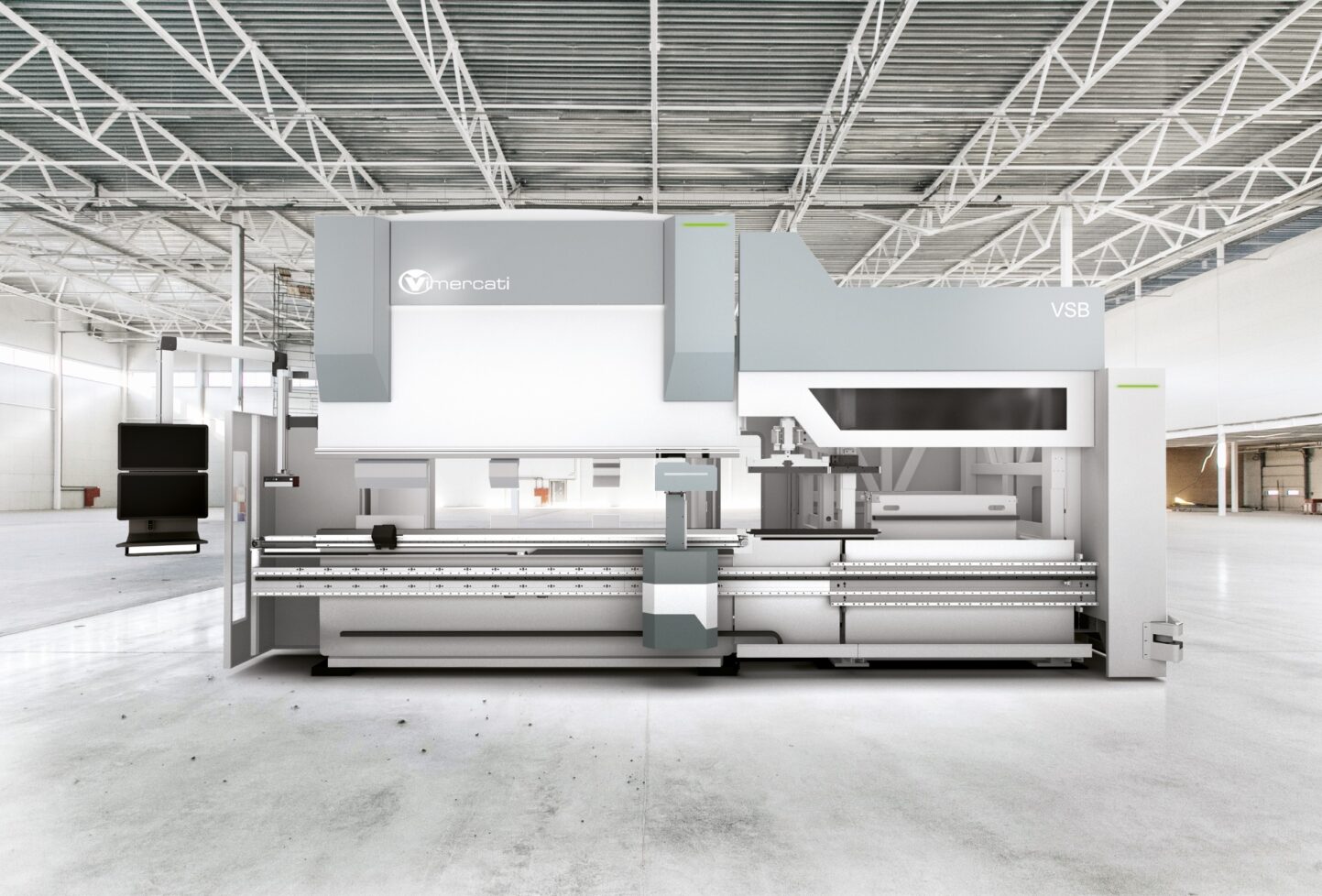
Optional: system to measure, check and correct the bending angle, the Laser Check Data M is set to obtain, right from the first piece, minimum precision tolerances regardless of any changes in thickness, strength and rolling direction of the material. The measuring sensors are located in metal casings for protection against any possible damage. They are motorized, have a side parking area, and entirely managed from the CNC. As soon as the bending sequence starts, the measurement sensors automatically align themselves with the piece to be bent to measure the angle, which can also be carried out in several points and wireless pedalboard: extremely user-friendly for operators, as there are no connecting cables.
Vimercati also offers robotized systems solutions such as the one presented at the fair at its stand. AkuBend robotic cell represents the most suitable solution to make the bending operations dynamic and flexible. An efficient, precise robotized bending cell with maximum automation optimization in terms of production batches and kind of product. Optimal for small batches and high variability, it is in fact possible to conciliate/gain with maximum simplicity an unattended automatic production with a production in manual mode of the press brake, through the automatic sliding of the press brake on the lateral rail system. In addition, the offline programming of the robot and press brake software eliminates the operator's checking and reprogramming times, that will only take care of the loading and unloading operations.
Still on the subject of automation, Vimercati also offers the VSB - Vimercati Storage Bend solution which consists in the integration of the press brake with an automatic tool changer warehouse. The VSB solution makes bending process more versatile, faster, and more reliable. It eliminates the manual configuration of the machine and allows the operator to dedicate their own time and skills in preparing the bending batches. It is ideal for small, complex, and uneven batches where setup times impact the productivity of the press brake and the production cost.